

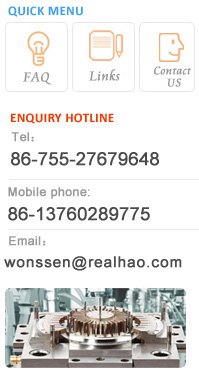
What is injection molding?
In injection molding, plastic granules are heated and "injected" under pressure into metal molds, where the molten plastic hardens into a designated shape. The mold then opens and the newly formed part is removed and inspected, ready for shipment or secondary manufacturing operations. Injection molding is an extremely versatile and popular form of molding. Other processes include extrusion, thermoforming, and blow molding.
What is insert molding?
Injection molding becomes insert molding when a specifically designed insert (typically of metal) is nested in the mold before the molten plastic is injected. The plastic hardens around the insert and the resulting part is a combination of plastic and insert. A simple example would be certain scissors in which metal blades are inserted into the mold, and plastic handles are molded around the blades.
What is an injection molding machine?
Broken down to its most fundamental components, an injection molding machine, or press, is comprised of three functional units: 1) injection (which melts and transmits the plastic granules), 2) mold (the custom designed portion which produces a specialized product,) and 3) clamping (which provides the controlled pressure to open and close the mold.) The following diagram, Figure 1, illustrates a simplified injection molding machine.
Penn Plastics is a full-service, family owned custom injection molder currently serving clients in a broad range of industries, including aerospace, automotive, consumer, industrial and medical.
What is a mold?
In injection molding, a mold is a specially designed metal tool consisting usually of a "mold base" and one or more "cavities". The cavities are contoured to the exact specifications of the desired product, and it is into these cavities that the molten plastic is forced and hardens. The cavities are situated in the mold base. A carefully engineered mold base will not only safely anchor and house the more delicate cavities, but will also provide for the quick and efficient production of a high quality part. Considerations for the design of a mold base include 1) the proper transmission of molten plastic along a system of channels (called "runners" - hot or cold), 2) the precise cooling and/or secondary heating necessary for a given part, and 3) the separating and ejecting of the part from the mold (and any runner) after it is complete. The following diagram, Figure 2, illustrates a simplified mold base.